铸钢材质解析:铁碳合金的铸造工艺与应用
19429202025-04-30医疗设备2 浏览
铁碳合金作为现代工业的基石,其铸造工艺与应用直接影响着机械制造、建筑工程等领域的核心部件性能。本文将从材质特性、铸造工艺、应用领域及常见问题四个维度展开解析,为行业从业者提供实用建议。
一、铁碳合金的材质特性与分类

铸钢是以铁和碳为主要元素的合金(碳含量通常为0.05%-2%),通过调整成分与工艺实现性能优化。
1. 核心元素的影响
碳(C):决定铸钢的强度与塑性。含碳量低于0.25%的低碳钢韧性优异,适用于焊接结构;0.25%-0.6%的中碳钢兼顾强度与塑性,广泛用于机械零件;高于0.6%的高碳钢则硬度高但脆性大,多用于耐磨部件。
硅(Si)与锰(Mn):硅提升流动性并减少铸造缺陷,锰则增强强度和细化晶粒。现代工艺中常通过提高锰含量(1%以下)替代高碳,以改善综合性能。
2. 铸钢与铸铁的差异
性能对比:铸钢强度、韧性优于铸铁,但成本更高;铸铁耐磨性和减震性更优,适合简单结构件。
适用场景:铸钢用于高压容器、铁路车轮等重载部件;铸铁则用于发动机缸体等对变形不敏感的场景。
3. 常见分类
按成分:铸造碳钢(低成本)、低合金钢(强度提升)、不锈钢(耐腐蚀)。
按用途:工程结构钢、工具钢(模具、刀具)、特种钢(耐高温、耐腐蚀)。
二、铸钢的铸造工艺优化要点
铸造工艺直接影响铸件的致密性、表面质量与力学性能,需从以下环节精细控制。
1. 熔炼与成分控制
原料选择:优先选用低硫磷废钢,减少杂质对性能的影响。
合金添加:铬、钼等元素可细化晶粒并提升耐热性,但需避免过量导致脆性。
2. 浇注工艺参数
温度:浇注温度一般高于熔点40-80℃。薄壁件需更高温度(1550-1600℃)以改善流动性,厚壁件可适当降低(1450-1500℃)减少缩孔。
速度:复杂件需快速浇注(20-30秒/吨)避免冷隔;大型件则需控制钢液上升速度(10-20 mm/s)防止气孔。
3. 冷却与后处理
顺序凝固:通过冒口与冷铁设计,使铸件从远端向冒口方向凝固,减少缩松。
热处理:正火处理可消除内应力,淬火+回火则提升硬度和韧性。
三、铸钢的核心应用领域与选材建议
铸钢凭借其性能优势,在多个工业场景中不可替代。
1. 重型机械
典型部件:轧钢机机架、水压机底座。
选材建议:ZG270-500(中碳钢)兼顾强度与成本,厚度超过200 mm时加入0.3%钼提升抗蠕变性。
2. 交通运输
典型部件:铁路车轮、船舶推进器。
选材建议:低碳合金钢(如ZG25CrMo)用于冲击载荷部件,表面渗碳处理提高耐磨性。
3. 能源与化工
典型部件:核电阀门、石油管道。
选材建议:奥氏体不锈钢(如ZG316L)用于腐蚀环境,耐热钢(ZG40Cr25Ni20)用于1000℃以上工况。
四、常见铸造缺陷与解决策略
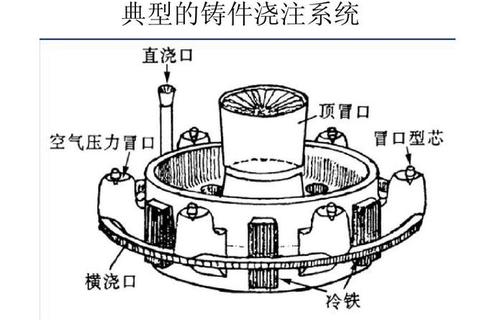
1. 缩孔与缩松
成因:凝固收缩未充分补缩。
对策:增加冒口体积(占铸件重量15%-20%),采用发热冒口延缓凝固。
2. 气孔与夹渣
成因:钢液含气量高或浇注卷入杂质。
对策:钢包吹氩脱气,浇注系统加设过滤网(孔径≤3 mm)。
3. 裂纹
成因:冷却不均或成分偏析。
对策:优化模具预热温度(200-300℃),限制硫磷含量(分别≤0.03%和0.035%)。
五、行业趋势与未来展望
1. 材料创新:高锰钢(Mn>12%)和纳米改性钢提升抗冲击性。
2. 工艺升级:3D打印砂型实现复杂结构一体化成型,减少后加工。
3. 智能化控制:光谱仪实时监测熔炼成分(如OE750系统),精度达0.001%。
实用建议清单
设计阶段优先选择标准化牌号(如ZG200-400),降低定制成本。
浇注前用红外测温仪校验钢液温度,偏差控制在±20℃以内。
定期校准模具尺寸,收缩率按1.8%-2.2%预留(厚大件取上限)。
通过材质优化与工艺精细化,铸钢件在强度、寿命和可靠性上将持续突破,为高端装备制造提供坚实支撑。